Asetek Stress Testing and Future Products
After learning about Asetek's innovative tubing for it closed-loop products, we were enthusiastically shown the extremes to which Asetek stress tests its designs. This testing is partly due to the company's focus on the OEM market, as system builders need to be sure the components they are using are as durable and reliable as possible. If your new Alienware rig gets filled with water when the cooler explodes, you’re probably not going to be buying another Alienware PC anytime soon, after all.
The freezing test it to ensure the coolers can cope with air freight. You can see the frost on the coolers
To this end Asetek has two temperature chambers, one which freezes the coolers down to nearly -30
oC to test that cooler designs are still functional after worst-case shipping and storage scenarios. The other chamber was set up to run extremely hot while the coolers were strapped to dummy CPU heat sources. This chamber was obviously to test that the coolers were capable of still cooling a CPU in the very worst of operating conditions.
Only designs that pass these stringent tests can make it to production stage and, as with many technology businesses, production duties are handled in China. This can pose a problem if any technical difficulties arise though, as problems in China are difficult to resolve from Denmark. To get around this problem Asetek has a mini production line built in the R&D centre. This allows Asetek to quickly get to the cause of any problems that might arise at the Chinese production plant.
Research and development involves both stress testing the coolers in extremely hot conditions (left) and experimenting with different fans and fin densities (right)
Asetek also showed us its airflow testing kit, which it uses for researching and assessing both the fans and radiators for its coolers. A fan or fan-and-radiator assembly is attached to the end plate of the test tube (the large blue tube in the pictures below) and the air speed and pressure is measured at various stages along the tube. This allows objective measurements on factors such as different fan speeds or different fin densities so that the final product carries the best balance of cooling potential and acoustic loveliness.
We were also given a little bit of an insight into some of the future products Asetek is working towards, with 92mm revisions of most of its lines either done or on the schedule. Though this is a minor revision, it's one that many OEMs requested as it’ll allow Asetek loops to be installed into smaller chassis not blessed with 120mm Fan mounts.
On the left is part of the Chinese production line mock-up. We'd like to say we got to take one of the coolers on the right home but we'd be lying
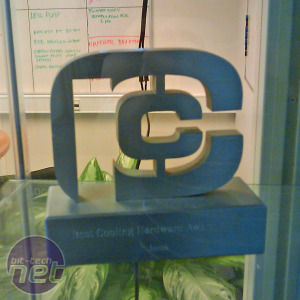
Asetek's trophy cabinet was stacked with prizes but
one stood above the rest.
We also quizzed Asetek on whether there were any plans to go larger with its LCLC coolers: with more and more cases coming with 140mm rear or roof fan mounts so it’d be a fairly logical progression. Nobody gave us an outright confirmation, but representatives did say they were aware of the trend and would be silly not to be looking at the possibility.
One thing the company was extremely tight lipped about was its
prototype all-in-one PC cooler that is claimed to be capable of cooling both an Intel Core i7 CPU and an Nvidia Geforce GTX 280 all in a compact all-in-one case. The cooler is only a prototype at this stage, but having the potential to put full-power desktop components into a compact all-in-one chassis is something to get excited about.
We'd like to thank Kenneth Knudsen from pcworld.dk (in Danish) for saving the day and letting us use some of his photos of the visit after our camera had a bad day. If you've got any comments, please post them in the forums.
Want to comment? Please log in.